Table of Contents
In today’s fast-paced business world, understanding and improving processes is key to success. One powerful tool that helps in this area is called SIPOC, which stands for Suppliers, Inputs, Process, Outputs, and Customers. This simple yet effective model gives a clear picture of a business process from start to finish.
SIPOC is not a new idea. It was first brought to light by Motorola in the 1980s and later gained more popularity through General Electric in the 1990s. This method is part of the Six Sigma approach, a set of techniques aimed at improving how businesses operate.
At its core, SIPOC helps teams and businesses see how their processes work in a straightforward way. It makes sure everyone involved understands the process the same way, which is crucial for making improvements. Whether you’re new to process management or looking to refine existing procedures, SIPOC is a valuable starting point. Let’s dive in and explore how SIPOC can make a difference in your business processes.
The Basics of SIPOC
SIPOC is a simple, yet powerful framework used to understand and document business processes. It stands for Suppliers, Inputs, Process, Outputs, and Customers. Each component plays a crucial role in mapping out how a process operates from beginning to end. Let’s break down these components to see what they mean:
Suppliers: These are the entities that provide the necessary resources for a process. Suppliers can be internal departments within a company or external organizations.
Inputs: Inputs are the materials, information, or resources provided by suppliers that are required to carry out the process.
Process: This is the series of steps or actions taken to transform inputs into outputs. A process can be anything from manufacturing a product to delivering a service.
Outputs: Outputs are the results or products of the process. They are what the process aims to produce or deliver.
Customers: Customers are the recipients of the outputs. Like suppliers, customers can be both internal and external to the organization.
Understanding SIPOC is essential for anyone looking to improve business processes. It helps clarify the flow of a process, making it easier to identify where changes can be made for improvement. By breaking down a process into these five components, teams can gain a high-level overview, which is the first step towards detailed analysis and optimization. Whether you’re looking to streamline operations, enhance quality, or reduce costs, starting with the basics of SIPOC is a smart move.
The Importance of SIPOC in Business Process Management
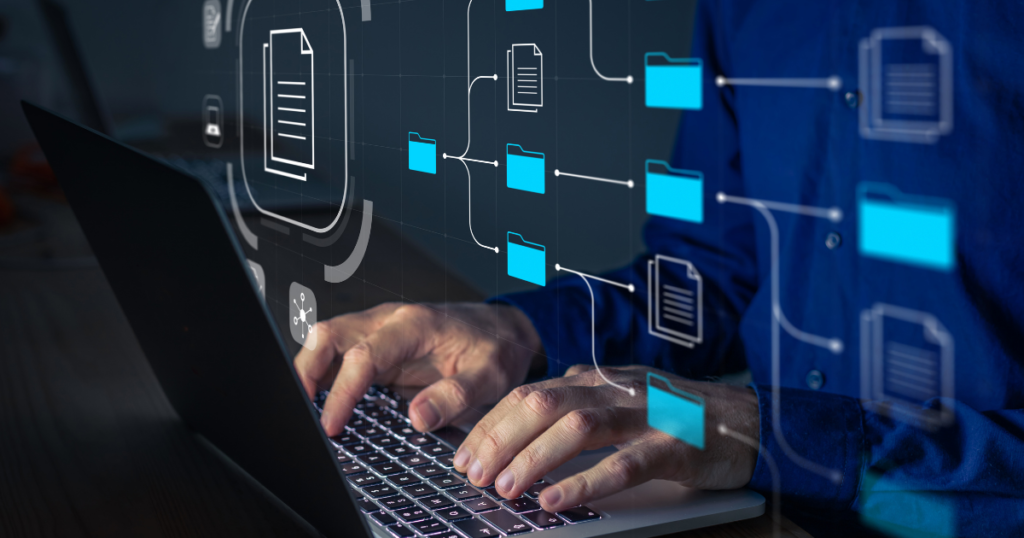
The SIPOC model is more than just a tool for mapping out processes. It plays a pivotal role in the management and improvement of business operations. Here’s why SIPOC is so important:
Clarity and Communication
One of the biggest challenges in any organization is ensuring everyone is on the same page. SIPOC provides a clear, concise overview of a process that can be understood by everyone involved, from team members to stakeholders. This clarity fosters better communication, as it eliminates confusion about what the process involves and who is responsible for what.
Identifying Improvement Areas
By laying out the key components of a process, SIPOC makes it easier to spot inefficiencies, bottlenecks, or areas that could benefit from optimization. With a high-level view, teams can quickly see which parts of the process need attention, leading to more targeted and effective improvements.
Facilitating Stakeholder Engagement
SIPOC diagrams are not just internal tools; they can also be shared with external stakeholders. This transparency helps build trust and ensures that everyone involved has a clear understanding of the process. Stakeholders can provide valuable feedback, which can be incorporated into process improvements.
Foundation for Detailed Analysis
While SIPOC offers a high-level overview, it also lays the groundwork for more detailed process analysis. Once the basic structure of a process is understood, teams can dive deeper into each component, using tools like flowcharts or value stream mapping to examine each step in detail.
In sum, the importance of SIPOC in business process management cannot be overstated. It brings clarity, facilitates communication, highlights areas for improvement, engages stakeholders, and serves as a foundation for further analysis. Whether you’re part of a small team or a large organization, incorporating SIPOC into your process management efforts can lead to significant benefits.
Creating a SIPOC Diagram
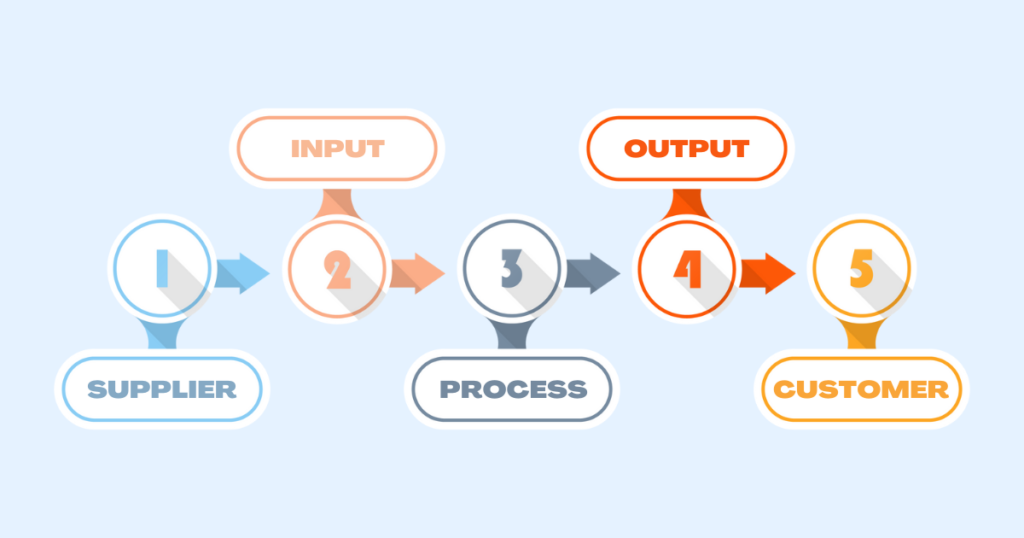
Creating a SIPOC diagram is a straightforward process that brings clarity and structure to understanding business operations. Here’s how you can create your own SIPOC diagram in a few simple steps:
Step 1: Identify the Process
Start by defining the process you want to analyze. It should be specific enough to be meaningful but broad enough to cover the essential steps. For instance, “processing customer orders” or “manufacturing product X.”
Step 2: List the Outputs
Think about the end results of the process. What are the key outputs? These could be physical products, services rendered, or information transferred. Listing the outputs first helps ensure that the process is customer-focused.
Step 3: Identify the Customers
Determine who receives the outputs of the process. Customers can be external clients who buy your product or service, or internal departments that rely on the outputs for their operations.
Step 4: List the Inputs
Consider what resources, materials, information, or other inputs are necessary for the process to happen. Inputs are what the process consumes to produce the outputs.
Step 5: Identify the Suppliers
Identify who or what provides the inputs listed in the previous step. Suppliers can be internal, like another department within your organization, or external, like vendors or partner companies.
Step 6: Map Out the Process
Outline the key steps or stages in the process. This doesn’t need to be a detailed workflow but should include the major phases or actions that transform inputs into outputs.
Tips for Creating a SIPOC Diagram:
- Keep it simple: The strength of a SIPOC diagram lies in its simplicity. Aim for a high-level overview rather than getting bogged down in details.
- Collaborate: Involve team members and stakeholders in the creation process. Different perspectives can help ensure nothing is overlooked.
- Use visual aids: Whether it’s a whiteboard, sticky notes, or diagramming software, visual tools can make the process more engaging and easier to understand.
Common Pitfalls to Avoid:
- Overcomplicating the diagram: Adding too much detail can make the SIPOC diagram overwhelming and less effective as a communication tool.
- Working in silos: Creating a SIPOC diagram in isolation can lead to gaps or inaccuracies. Collaboration is key.
- Neglecting validation: Once your SIPOC diagram is complete, review and validate it with those who are involved in the process to ensure accuracy.
Creating a SIPOC diagram is an essential first step in understanding and improving business processes. By following these steps and tips, you can develop a clear, comprehensive view of how your processes work, setting the stage for further analysis and optimization.
SIPOC in Different Industries
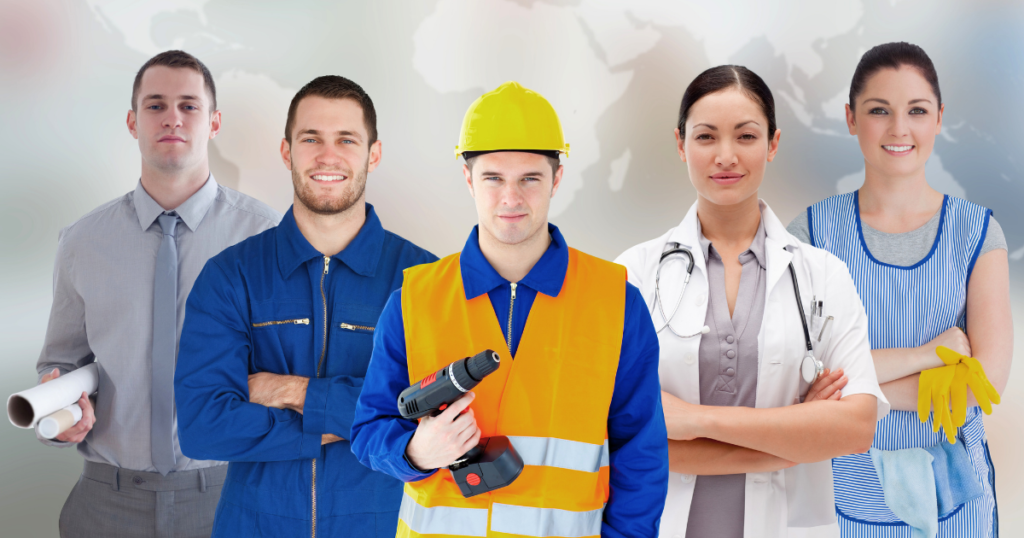
The versatility of the SIPOC model makes it a valuable tool across a wide range of industries. Whether in manufacturing, services, healthcare, or education, SIPOC helps organizations understand and improve their processes. Let’s explore how SIPOC is applied in different sectors:
Manufacturing
In the manufacturing industry, SIPOC is critical for ensuring product quality and efficiency. Here, the focus is often on the traditional sequence of Suppliers, Inputs, Process, Outputs, and Customers (SIPOC). This approach helps in identifying the raw materials (Inputs) needed, the suppliers of those materials, the manufacturing process itself, the final products (Outputs), and the customers who receive them. By analyzing these components, manufacturers can pinpoint inefficiencies, reduce waste, and optimize production lines for better performance.
Service Industry
The service sector, including businesses like restaurants, banks, and IT companies, often employs the COPIS approach, where the focus starts with the Customers and works backward. This customer-centric model ensures that services are designed and delivered according to customer needs and expectations. For example, a restaurant would start by considering the customer’s dining experience (Customer), what dishes are offered (Outputs), how those dishes are prepared (Process), what ingredients are needed (Inputs), and who supplies those ingredients (Suppliers).
Healthcare
In healthcare, SIPOC diagrams help streamline patient care processes, administrative tasks, and other critical functions. By mapping out processes such as patient admission, treatment protocols, or billing, healthcare providers can identify areas for improvement, enhance patient care, and increase operational efficiency. SIPOC also plays a role in ensuring compliance with healthcare regulations and standards.
Education
Educational institutions use SIPOC to enhance both administrative and educational processes. From student enrollment and course delivery to research and campus management, SIPOC helps identify the key elements of each process, ensuring that resources are allocated efficiently and that educational outcomes meet both student and institutional expectations.
Information Technology (IT)
In IT, SIPOC diagrams are used for software development, network management, and service delivery processes. They help clarify the requirements (Inputs) from various stakeholders (Suppliers), outline the development or management processes, specify the deliverables (Outputs), and identify the end-users (Customers). This clarity is crucial for managing complex IT projects and ensuring they meet user needs.
Key Takeaways:
- Adaptability: SIPOC’s framework is flexible and can be adapted to the unique needs and focus of different industries.
- Customer Focus: Whether using the traditional SIPOC or the COPIS variation, the model emphasizes understanding and meeting the needs of the customer.
- Process Improvement: Across all industries, SIPOC is a tool for identifying inefficiencies and areas for process improvement.
In conclusion, SIPOC’s applicability across various industries highlights its value as a universal tool for process analysis and improvement. By adapting the model to fit specific industry needs, organizations can gain insights into their operations, leading to enhanced efficiency, customer satisfaction, and overall performance.
The Benefits of Implementing SIPOC
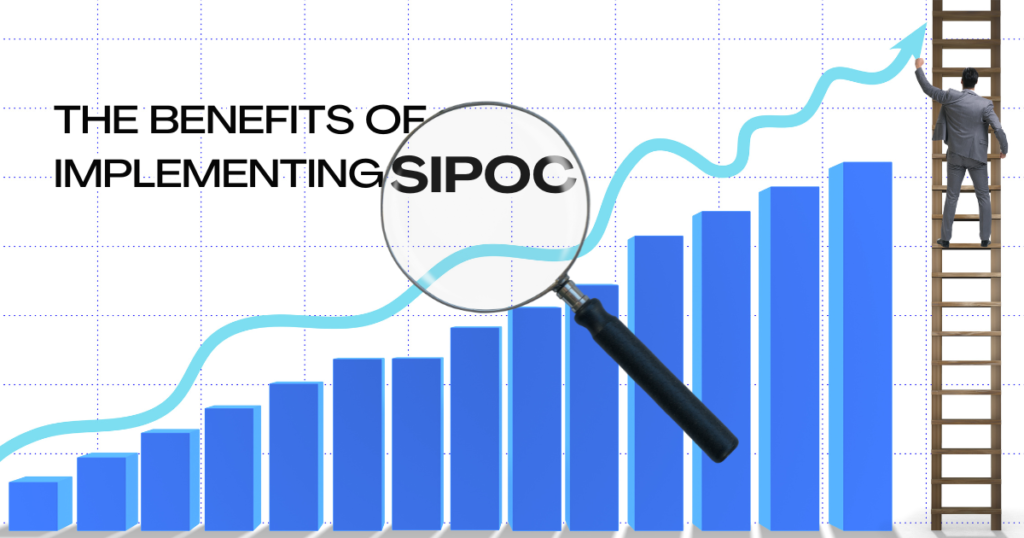
Implementing the SIPOC model in your business processes can bring about a multitude of benefits. This simple yet effective tool not only enhances understanding and communication but also drives significant improvements in various aspects of operations. Below are some of the key advantages of using SIPOC:
Enhanced Clarity and Understanding
One of the primary benefits of a SIPOC diagram is that it provides a clear, high-level overview of a process. This clarity is invaluable for new employees, stakeholders, and even seasoned team members who need a refresher. Understanding the flow from suppliers to customers helps everyone grasp their role in the process and see how their contributions fit into the bigger picture.
Improved Communication
SIPOC fosters better communication within teams and across departments. By laying out the key components of a process, it eliminates ambiguity and ensures that everyone is speaking the same language. This shared understanding makes it easier to discuss improvements, address issues, and collaborate more effectively.
Identification of Key Areas for Improvement
With its straightforward structure, SIPOC helps identify inefficiencies, bottlenecks, or areas that lack clarity. By highlighting these areas, organizations can prioritize where to focus their improvement efforts. This targeted approach leads to more efficient processes, reduced costs, and improved quality.
Facilitates Stakeholder Engagement
Sharing SIPOC diagrams with stakeholders, including customers and suppliers, can enhance engagement and collaboration. It provides a transparent view of the process, inviting feedback and suggestions. This open line of communication can lead to innovative solutions and stronger partnerships.
Foundation for Further Analysis
While SIPOC provides a high-level view, it also sets the stage for deeper analysis. Once the basic elements of a process are mapped out, teams can delve into each component with tools like flowcharts, lean management techniques, or Six Sigma methodologies. SIPOC is often the first step in a comprehensive process improvement journey.
Streamlined Process Management
By understanding the inputs, outputs, and steps involved in a process, organizations can streamline operations, eliminate unnecessary steps, and optimize resources. This streamlined approach can lead to faster turnaround times, increased productivity, and better overall performance.
Enhanced Customer Satisfaction
Ultimately, the insights gained from implementing SIPOC can lead to improvements that enhance customer satisfaction. Understanding and meeting customer needs more efficiently can lead to higher quality products and services, timely delivery, and improved customer experience.
In summary, implementing SIPOC in your business processes can lead to significant benefits, including enhanced clarity, improved communication, focused improvement efforts, and ultimately, higher customer satisfaction. Whether you’re looking to refine existing processes or implement new ones, SIPOC is a valuable tool in your process improvement toolkit.
SIPOC and Continuous Improvement
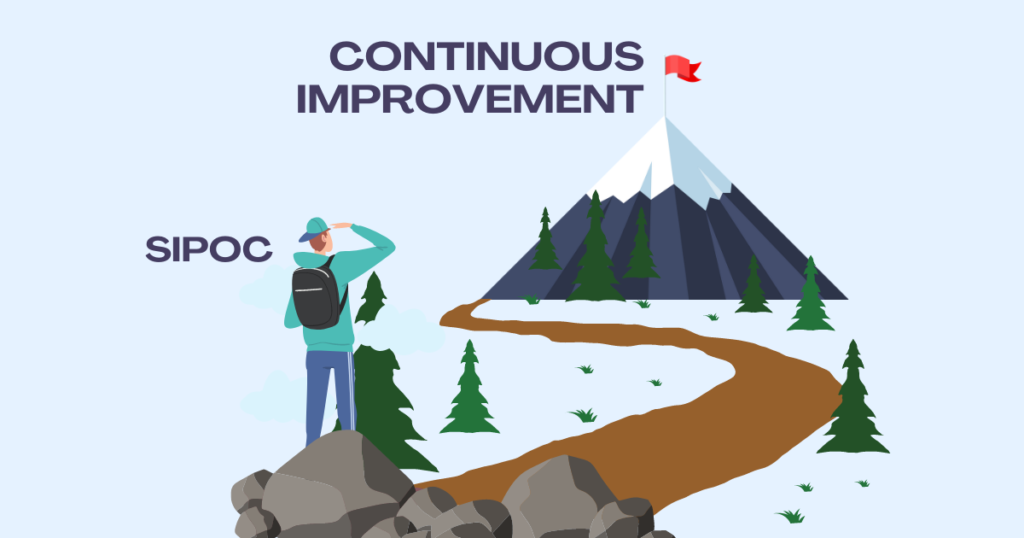
The SIPOC model is not just a tool for mapping out processes; it’s also a catalyst for continuous improvement within an organization. By providing a clear framework for understanding the relationships between suppliers, inputs, processes, outputs, and customers, SIPOC lays the groundwork for ongoing enhancements. Here’s how SIPOC contributes to a culture of continuous improvement:
Identifying Improvement Opportunities
SIPOC diagrams make it easier to see the entire process at a glance, from the beginning to the end. This visibility helps teams identify inefficiencies, bottlenecks, and areas where resources may be wasted. By pinpointing these opportunities, organizations can develop targeted strategies for improvement.
Enhancing Process Efficiency
Once potential areas for improvement are identified, SIPOC can guide the prioritization and implementation of changes designed to enhance efficiency. Whether it’s streamlining the flow of inputs, optimizing the process steps, or improving the quality of outputs, SIPOC helps ensure that efforts are focused where they can have the most significant impact.
Facilitating Root Cause Analysis
Continuous improvement often involves digging deeper into issues to understand their root causes. SIPOC diagrams provide a high-level overview that can be the starting point for more detailed analyses, such as the Five Whys or fishbone diagrams. Understanding the root causes of inefficiencies or quality issues is crucial for developing effective solutions.
Supporting the DMAIC Process
In the context of Six Sigma, SIPOC is particularly valuable during the Define and Measure phases of the DMAIC (Define, Measure, Analyze, Improve, Control) methodology. By defining the process and its key components, teams can more accurately measure performance, analyze process variations, and implement improvements that are controlled and monitored for effectiveness.
Encouraging Stakeholder Collaboration
Continuous improvement is a team effort, and SIPOC diagrams serve as a common language that facilitates collaboration among all stakeholders. By involving suppliers, team members, and customers in the improvement process, organizations can gather diverse insights and ideas, leading to more innovative and effective solutions.
Driving a Culture of Improvement
Implementing SIPOC and using it as a basis for continuous improvement initiatives helps instill a culture of quality and efficiency. When teams regularly use SIPOC to assess and improve their processes, it reinforces the importance of always looking for ways to do things better, faster, and more cost-effectively.
Monitoring and Adjusting Processes
Continuous improvement is an ongoing cycle, and SIPOC diagrams can be updated and adjusted as processes evolve. This adaptability ensures that improvements are sustained over time and that processes remain aligned with changing business objectives and customer needs.
In conclusion, SIPOC is a powerful tool that supports continuous improvement by providing clarity, facilitating analysis, encouraging collaboration, and driving a culture of ongoing enhancement. By integrating SIPOC into their continuous improvement efforts, organizations can achieve significant gains in efficiency, quality, and customer satisfaction.
Beyond SIPOC – Six Sigma Certification
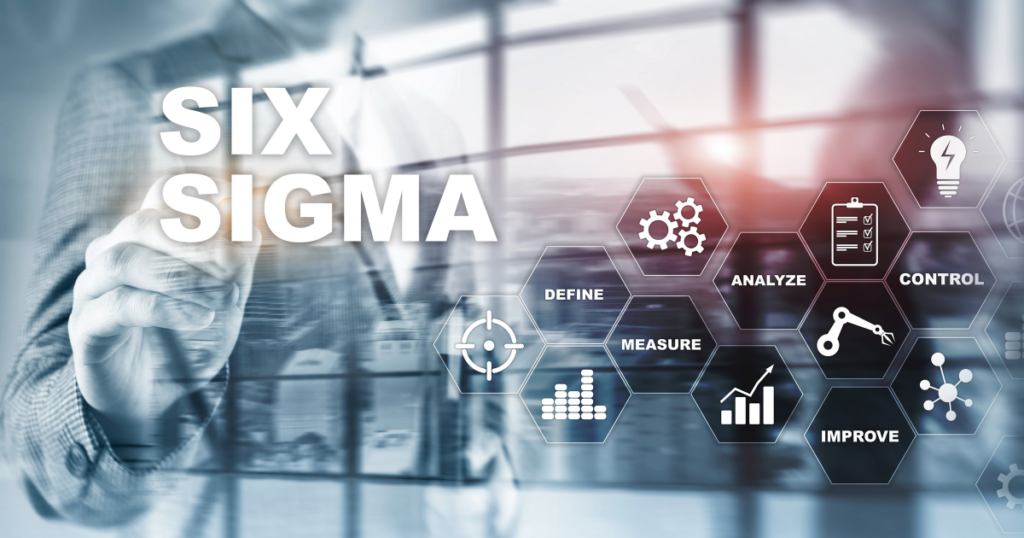
While the SIPOC model is a valuable tool for understanding and improving business processes, it’s just one component of a broader methodology known as Six Sigma. For professionals looking to deepen their expertise in process improvement, pursuing Six Sigma certification can be a significant next step. Here’s why Six Sigma certification is worth considering and how it complements the foundational knowledge provided by SIPOC:
Understanding Six Sigma Certification
Six Sigma is a data-driven approach to eliminating defects and improving processes in any business operation. Certification in Six Sigma is offered at various levels, each denoting a different degree of expertise:
- Yellow Belt: For those new to the world of Six Sigma who need a basic understanding of the principles and key tools.
- Green Belt: For professionals who lead small-scale improvement projects and assist Black Belt leaders in more complex projects.
- Black Belt: For experts who lead project teams and are proficient in Six Sigma methodologies and tools.
- Master Black Belt: For top-level professionals who develop strategies, mentor Black and Green Belts, and drive innovation within an organization.
Benefits of Six Sigma Certification
- Enhanced Problem-Solving Skills: Six Sigma training equips individuals with a robust set of tools and techniques for identifying, analyzing, and solving quality and efficiency problems.
- Career Advancement: Being certified in Six Sigma is highly regarded in various industries and can open doors to leadership and management positions.
- Improved Process Quality: Six Sigma’s focus on statistical analysis and quality control leads to significant improvements in processes and products.
- Increased Customer Satisfaction: By reducing defects and improving processes, organizations can deliver higher quality products and services, leading to greater customer satisfaction.
- Operational Excellence: Six Sigma principles promote a culture of continuous improvement, driving operational efficiency and excellence across the organization.
How Six Sigma Certification Complements SIPOC
Six Sigma certification provides a deeper dive into the methodologies and tools for process improvement, including but not limited to SIPOC. While SIPOC offers a high-level overview of processes, Six Sigma training teaches how to apply statistical analysis and other techniques to precisely measure and improve those processes. In essence, SIPOC can be seen as the starting point, and Six Sigma certification provides the knowledge and skills to take process improvement to the next level.
Getting Started with Six Sigma Certification
For those interested in pursuing Six Sigma certification, there are numerous resources available, including online courses, in-person training programs, and study guides. Organizations like ASQ (American Society for Quality) and IASSC (International Association for Six Sigma Certification) are reputable sources for certification information and resources.
In conclusion, while SIPOC is an excellent tool for mapping out and understanding processes, Six Sigma certification offers a pathway to mastering the art and science of process improvement. Whether you’re aiming to enhance your career, contribute to your organization’s success, or simply learn more about effective process management, Six Sigma certification is a valuable investment in your professional development.
Conclusion
The journey through understanding and utilizing the SIPOC model reveals its simplicity and power as a tool for enhancing business processes. From its origins in Six Sigma methodology to its application across various industries, SIPOC serves as a foundational element for identifying, analyzing, and improving the flow of work. It provides a clear, high-level view of processes, ensuring that everyone involved—from team members to stakeholders—has a common understanding of how operations unfold from suppliers to customers.
Implementing SIPOC brings numerous benefits, including improved clarity and communication, identification of key areas for improvement, and the facilitation of stakeholder engagement. It sets the stage for continuous improvement by highlighting inefficiencies and providing a structured approach to addressing them. Moreover, SIPOC is not just a standalone tool; it is a stepping stone towards deeper process analysis and improvement methodologies, such as those offered by Six Sigma certification.
For professionals looking to enhance their skills in process management and improvement, delving beyond SIPOC into Six Sigma certification offers a path to greater expertise and career advancement. Six Sigma’s rigorous approach to eliminating defects and optimizing processes complements the foundational insights provided by SIPOC, enabling individuals to drive significant improvements in quality, efficiency, and customer satisfaction.
In essence, the SIPOC model is more than just a diagram; it’s a catalyst for change. Whether you’re a beginner in the world of process improvement or a seasoned professional seeking to refine your skills, the principles encapsulated in SIPOC and Six Sigma provide a robust framework for achieving operational excellence. By embracing these tools and methodologies, organizations and individuals can navigate the complexities of business processes with confidence, paving the way for sustained success and continuous growth.
Additional Resources
For those interested in diving deeper into the SIPOC model, Six Sigma, and process improvement methodologies, a wealth of resources is available. Here is a curated list of resources to further your understanding and application of these powerful tools:
Books
Online Courses
Coursera offers various courses on Six Sigma and process improvement, including Six Sigma Yellow Belt and Green Belt certification prep courses.
- Leading Business Improvement by Robert Chapman
- Udemy also provides a range of Six Sigma courses tailored to different levels of expertise, from beginners to advanced practitioners.
- ASQ (American Society for Quality) offers comprehensive Six Sigma training and certification programs for all belt levels.
Websites and Online Resources
iSixSigma – A rich repository of articles, tools, and forums dedicated to Six Sigma practitioners.
Templates and Tools
Lucidchart and Miro – Online platforms that offer SIPOC diagram templates and collaborative tools for process mapping.
Professional Organizations
American Society for Quality (ASQ) – A global community of quality professionals offering certifications, training, and knowledge on quality improvement practices.
International Association for Six Sigma Certification (IASSC) – Provides globally recognized Six Sigma certification exams and resources.
These resources can provide valuable insights and tools for individuals and organizations looking to implement the SIPOC model and embrace Six Sigma methodologies. Whether you’re seeking to gain certification, improve your organization’s processes, or simply expand your knowledge, these resources offer a pathway to achieving operational excellence and quality improvement.