Table of Contents
Why the Yellow Belt Deserves More Hype
Most people think the Lean Six Sigma Yellow Belt is just an entry-level certificate. A nice-to-have. Something you get before you move on to the “real” stuff like Green or Black Belt.
That thinking is wrong.
Yellow Belt is more than a course. It’s a shift in how you approach problems. It teaches you to see what’s broken in everyday work, not just guess — but know — how to fix it. It gives structure to chaos and shows you how small changes can make a big difference.
This certification may not make headlines, but it’s the foundation that holds up major process improvements in companies worldwide. It’s the reason why project delays shrink, waste drops, and teams stop spinning their wheels.
And here’s the real deal: employers notice Yellow Belts. According to ZipRecruiter, Yellow Belt holders in the U.S. earn an average salary of around $97,000. That’s not entry-level pay — that’s what problem solvers earn.
So no, it’s not “just a beginner cert.” It’s the toolkit that turns average employees into go-to problem fixers. It’s where lean thinking begins — and where better business starts.
The Hidden Everyday Problems Only Yellow Belts Know How to Solve
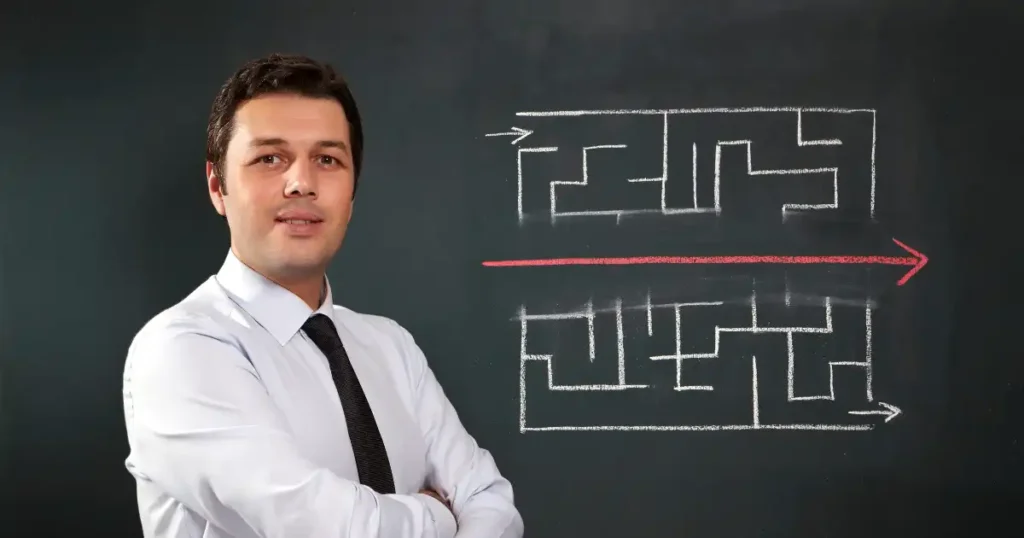
Ever seen the same mistake happen five times in one week?
Maybe it’s a wrong file name sent to a client. Or a delivery team using outdated instructions. You fix it once, twice — then stop bothering because “that’s just how it is.”
That mindset costs businesses time, money, and trust. That’s exactly where a Yellow Belt steps in.
Unlike most employees who react to problems, Yellow Belts are trained to find out why the issue keeps coming back. They use proven tools like the 5 Whys and fishbone diagrams to dig deeper, identify the root cause, and fix it for good. Not with guesses — with data.
Let’s look at a real example.
A logistics company had drivers repeatedly missing scheduled pickups. Managers assumed it was poor performance. A Yellow Belt on the team did a quick process map and discovered the problem was with the printed schedule — it was often wrong by an hour. Fixing the scheduling system took less than a week. That one change saved over 15 hours a week, improved client satisfaction, and boosted morale on the floor.
That’s the power of Yellow Belt thinking — small changes, big outcomes. Where others see a messy problem, Yellow Belts see a system waiting to work better.
Why Companies Actually Prefer Yellow Belts Over “Experts”
Companies don’t just want experts. They want people who can get things done.
That’s where Yellow Belts shine.
They bring just the right amount of structure to messy workflows. They’re not buried in theory. They don’t waste time building overcomplicated models. Yellow Belts know enough Lean Six Sigma to improve real-world problems — fast and with focus.
They understand the basics: DMAIC (Define, Measure, Analyze, Improve, Control), process mapping, root cause analysis, and waste reduction. That’s more than enough to clean up bottlenecks, fix repetitive mistakes, and reduce costs without getting lost in jargon.
That’s why companies in manufacturing, healthcare, finance, IT, logistics, and even HR actively train Yellow Belts. These industries need cross-functional problem-solvers who can work inside teams and apply Lean thinking without disrupting everything else.
A 2022 study by GoLeanSixSigma found that Yellow Belts contributed to over 60% of completed improvement projects in mid-sized companies. Why? Because they’re embedded in operations. They see issues as they happen and have the tools to fix them before they grow.
In short, Yellow Belts don’t over-engineer. They act. That makes them more valuable, more versatile, and more reliable than many so-called “experts” who never leave the whiteboard.
What’s in It for You? Salary, Skills & Serious Leverage

Let’s talk money.
According to ZipRecruiter, Lean Six Sigma Yellow Belt professionals in the U.S. earn an average of $97,000 per year. Entry-level salaries typically start around $50,000–$65,000, and experienced professionals can push well past $90,000. That’s serious value for a certification that takes just a few days to complete.
But salary is only part of the picture.
The real power of Yellow Belt training is in the skills you build — skills most employees never learn. You become someone who knows how to make sense of messy processes, fix what’s broken, and prove the results. That’s problem-solving confidence most people fake.
And when you consistently solve problems? You earn respect. Teams start looking to you for input. Managers notice. You move from support role to decision-maker — not because you asked, but because you earned it.
In tight job markets, certifications are tiebreakers. When two candidates look the same on paper, the one with Lean Six Sigma training stands out. It signals you’re not just a worker — you think in systems, understand processes, and can help any team run better.
The Yellow Belt may be small, but the impact is outsized. It puts you in a position of influence — not someday, but now.
Yellow Belts Are the Project Underdogs That Deliver Big Wins
Yellow Belts rarely lead projects — but they often make or break them.
In Six Sigma teams, Green and Black Belts usually run the show. They plan, lead, and manage improvement efforts. But behind every successful project is a group of Yellow Belts doing the groundwork: collecting data, mapping processes, spotting waste, and testing solutions.
They’re the connective tissue between strategy and execution. They know the process firsthand. They work where the problems actually happen. That makes them essential.
Yellow Belts simplify what others complicate. While senior project leads might focus on performance metrics and advanced analytics, Yellow Belts help translate those into real changes on the floor.
Take this example: A manufacturing plant had issues with packaging errors — mislabeled boxes, missing items, late shipments. A Yellow Belt on the line suggested a color-coded checklist at each station. Simple, low-tech, but effective. Within three weeks, packing errors dropped by 40%. No new software. No consultants. Just smart observation and fast action.
This is the marginal gains mindset: fix the small things that slow you down. And when you fix enough of them, the results compound.
So while Yellow Belts might not wear the title of “project lead,” they deliver the outcomes that make projects succeed. They’re the underdogs — and they’re the ones who quietly keep things moving forward.
The Fastest Way to Get into Continuous Improvement Culture
The Lean Six Sigma Yellow Belt is one of the quickest, most practical certifications you can earn — typically in just 2 to 3 days. No prior experience required. No steep learning curve. And the return on that short investment? Immediate.
Companies love Yellow Belts because they’re fast to train and fast to contribute. You don’t need months of deep-dive analysis to start making a difference. With basic tools like DMAIC, process maps, and cause-and-effect analysis, Yellow Belts can identify inefficiencies and suggest improvements within weeks of getting certified.
That’s how continuous improvement takes hold — from the ground up, not just from the top down. Senior leaders might set the goals, but it’s people on the floor, in the office, and on the front lines who see the problems first. Yellow Belts become the eyes and ears of change.
That’s also why companies prefer to train dozens of Yellow Belts instead of only a handful of Green or Black Belts. More Yellow Belts mean more people speaking the same improvement language, spotting issues early, and taking ownership of results. It builds a culture where everyone contributes to getting better — every day.
For individuals, the low cost, short duration, and high impact make it a no-brainer. For companies, it’s the cheapest, fastest way to make continuous improvement part of the DNA.
Compliance, Credibility & Career Armor
In regulated industries, mistakes aren’t just costly — they’re risky.
Whether it’s healthcare, finance, manufacturing, or logistics, organizations need to stay compliant with strict quality standards. That’s where Yellow Belts come in.
Trained in process control, error reduction, and documentation standards, Yellow Belts help teams catch problems before they become violations. They know how to build repeatable processes that meet internal policies and external regulations — from ISO 9001 to FDA requirements.
In effect, Yellow Belts act as guardrails. They don’t just do the work — they keep it aligned with what’s safe, legal, and quality-approved.
And this credibility stretches beyond Six Sigma roles. In product management, Yellow Belt skills mean you ship better, faster. In HR, you optimize onboarding or performance review processes. In operations, you cut delays and waste with data-backed fixes.
No matter the role, Yellow Belt training sends a clear message: you understand structure, you respect process, and you know how to drive quality. That’s career armor in any department — and it only makes you harder to replace.
What to Do After Getting Certified (Spoiler: Don’t Stop Here)
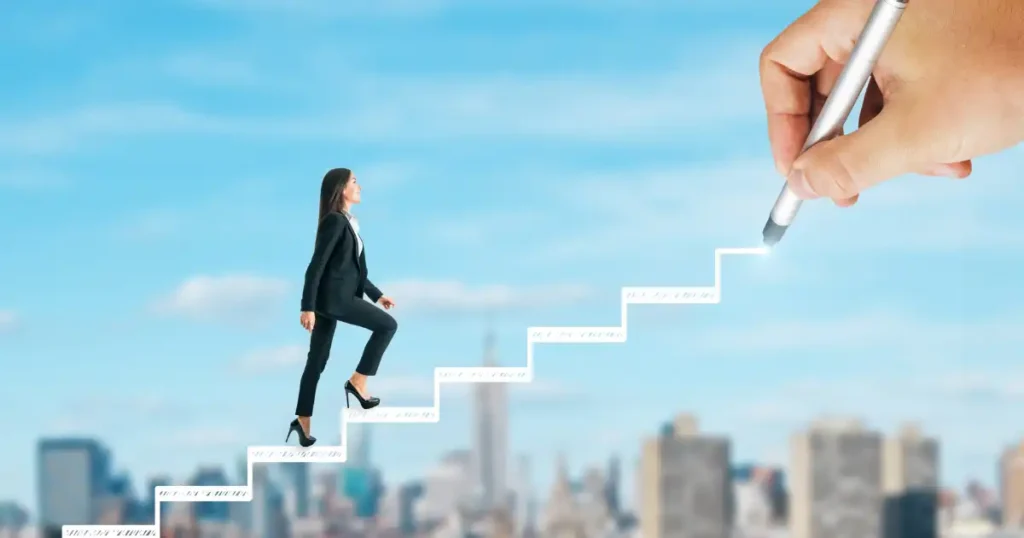
Getting your Yellow Belt isn’t the finish line. It’s the launch pad.
Once certified, you’ve got the fundamentals — now it’s time to use them. Start by looking at your current role. Where are the repeat issues? What slows your team down? Apply basic tools like process maps, 5 Whys, or Pareto charts to small problems. Even simple improvements can lead to noticeable wins.
Then, look outward. Join a Green or Black Belt-led project. Volunteer to assist with data collection or process reviews. You’ll gain hands-on experience while learning how more advanced projects work. That exposure is key if you plan to move up.
Next stop: Green Belt. While Yellow Belts focus on local, team-level problems, Green Belts lead full-scale improvement projects. Black Belts go even further — driving cross-functional change, leading teams, and training others.
Beyond skills, there’s also a community. Lean Six Sigma isn’t just a method — it’s a global network of professionals across industries. Joining that network gives you access to shared tools, project templates, case studies, and job opportunities. You learn the language of improvement — and people who speak it recognize you.
So don’t let your Yellow Belt gather dust. Use it. Build on it. Grow with it. It’s your first step into a bigger world where better processes mean better careers.
Why Yellow Belts Don’t Wait for Change — They Drive It
The Lean Six Sigma Yellow Belt isn’t just a step up the career ladder — it’s a step into work that actually matters.
You’re not waiting for someone else to fix the problems. You’re trained to see waste, find causes, and solve issues that everyone else just works around. You make things better — not someday, but today.
That’s the power of the Yellow Belt. It turns you from a passive participant into an active problem-solver. From someone who follows the process to someone who improves it.
So here’s the move: don’t overthink it. Start with the problems that bug you most — missed deadlines, repeat errors, inefficient handoffs. Apply the tools. Show results. Build momentum.
Pick a course. Get certified. Be the person who makes work smoother, smarter, and more efficient.
Your team doesn’t just need more help. They need a process hero. And that starts with Yellow.
Lean Six Sigma Yellow Belt Certification Course
Buy Now for £12.99
Udemy prices may vary depending on applied coupons and promotional events.
- 🧑🏫 136 lectures
- ⌚ 10h 55m total length
- 🗃️ 31 downloadable resources
- 📜 Certificate of completion
- 👩🎓 11,951 students
- ⭐ 4.6 rating by 671 students