FMEA: Failure, Modes, Effects, Analysis | Certification Course
Buy Now for $13.99
Udemy prices may vary depending on applied coupons and promotional events.
- 🧑🏫 29 lectures
- ⌚ 2h 3m total length
- 🗃️ 6 downloadable resources
- 📜 Certificate of completion
- 👩🎓 12,634 students
- ⭐ 4.7 rating by 482 students
We offer a detailed breakdown of RPN in our highest-rated Failure Modes and Effects Analysis (FMEA) course on Udemy. If you’re interested in exploring other tools within the FMEA methodology, consider enrolling in our course.
Table of Contents
1. Introduction to FMEA
Failure Mode and Effects Analysis (FMEA) is a cornerstone methodology in modern risk management and quality assurance. It offers a systematic approach to identifying potential failures in products, processes, and systems—long before they lead to real-world issues. But how did this powerful tool come into being, and why is it so essential today?
A Brief History of FMEA
FMEA was first developed by the U.S. military in the 1940s, aiming to improve the reliability of complex systems during World War II. Its systematic approach gained momentum in the 1960s when NASA adopted it during the Apollo space missions. According to NASA engineers, “Every failure could mean a billion-dollar mission and lives at stake, so we had to foresee problems before they happened.” This mindset brought FMEA into industries like aerospace, automotive, and manufacturing, where reliability and safety are paramount.
Fast forward to today, FMEA has become a global standard for risk assessment across sectors, including healthcare, software development, and renewable energy. Its evolution has been fueled by the need for proactive measures in a world where a single failure can ripple across global supply chains.
What is FMEA? Key Terms Explained
At its core, FMEA breaks down potential risks into manageable components:
- Failure Mode: The ways a product or process might fail, such as a cracked part or a delayed process step.
- Effects: The consequences of these failures on customers, systems, or operations, ranging from minor inconveniences to catastrophic impacts.
- Criticality: A ranking system to prioritize issues based on their severity, occurrence, and detectability.
- Analysis: A structured examination of these risks to mitigate or eliminate them.
Simply put, FMEA is like a safety net—it catches vulnerabilities before they escalate into disasters.
Why FMEA Matters in Today’s World
In an era of rapid innovation and interconnected systems, FMEA is critical for ensuring quality, reliability, and customer satisfaction. A 2019 report by the Automotive Industry Action Group (AIAG) revealed that companies using FMEA reduced product defects by over 70%. By addressing risks early, organizations save time, money, and reputational damage.
A Fresh Perspective: FMEA Meets AI
What’s exciting is the integration of FMEA with modern technologies like artificial intelligence (AI) and data analytics. Tools powered by AI can sift through vast datasets to predict failure patterns with unprecedented accuracy. Imagine using machine learning to not only identify potential failures but to also recommend actionable solutions—this is the future of FMEA.
Whether you’re designing the next Mars rover or a smartphone app, FMEA is your blueprint for proactive risk management. In this blog, we’ll dive deep into its types, methodologies, and advanced applications, ensuring you’re equipped with the knowledge to stay ahead. Let’s get started!
2. Types of FMEA and Their Applications
Failure Mode and Effects Analysis (FMEA) comes in two primary types: Design FMEA (DFMEA) and Process FMEA (PFMEA). Each serves a unique purpose in identifying and mitigating risks at different stages of product or process development. Let’s break down these types and explore their applications in real-world scenarios.
2.1 Design FMEA (DFMEA)
Design FMEA focuses on analyzing potential failures during the design phase of a product. It’s all about ensuring that the product will perform as intended under all conditions, addressing risks such as material defects, design flaws, or component malfunctions before production begins. By identifying these risks early, organizations can save significant costs associated with recalls, redesigns, or warranty claims.
Key Areas of Focus:
- Material Properties: For example, will the chosen material withstand expected stress, temperature, or wear?
- Geometry and Tolerances: Are the dimensions and tolerances suitable to ensure proper fit and function?
- Interactions with Other Components: How will this part or subsystem interact with other parts or systems? Could there be misalignments or interferences?
- External Factors: How will environmental conditions, such as humidity or extreme temperatures, impact the product?
Industries That Rely on DFMEA
- Automotive: Ensuring the safety and reliability of vehicles by addressing design flaws in brakes, engines, or suspension systems.
- Aerospace: Guaranteeing the structural integrity of aircraft components under extreme conditions.
- Consumer Electronics: Minimizing risks like overheating, short circuits, or software malfunctions in devices like smartphones and laptops.
Hypothetical Example
Imagine a team designing an electric vehicle battery. During the DFMEA process, they identify a potential failure mode: overheating during rapid charging. The effect could be battery degradation or, in severe cases, fire. Severity is ranked high due to safety concerns. By digging into root causes, they discover that inadequate heat dissipation in the design is the culprit. The solution? Adding thermal management systems, such as heat sinks or improved ventilation, and validating these changes through testing. This proactive approach prevents safety hazards and costly recalls.
2.2 Process FMEA (PFMEA)
While DFMEA addresses risks in the product’s design, Process FMEA focuses on failures that might occur during manufacturing or assembly. It’s about ensuring that production processes consistently produce quality products while minimizing defects, downtime, and safety risks.
Key Areas of Focus:
- Human Factors: How likely is operator error, and how can processes be designed to reduce it?
- Machinery Reliability: Are there risks of equipment failure? Are maintenance schedules sufficient to prevent breakdowns?
- Environmental Influences: Could factors like dust, temperature, or humidity impact production outcomes?
Industries That Rely on PFMEA
- Automotive Manufacturing: Ensuring processes like welding or painting are consistent and defect-free.
- Pharmaceuticals: Maintaining cleanliness and precision in drug production to avoid contamination.
- Food Processing: Identifying risks in packaging lines, such as improper sealing, to ensure product safety and freshness.
Case Study: Assembly Line Optimization
A factory producing smartphones uses PFMEA to analyze its assembly line. A potential failure mode is identified: misalignment of camera modules during installation. The effects include defective products and customer dissatisfaction. Occurrence is ranked as moderate, as the issue is linked to operator fatigue during manual assembly.
The team investigates root causes and discovers that manual handling and repetitive motion are the primary factors. They implement automated robotic arms to handle camera placement, paired with vision systems to detect misalignments in real-time. Additionally, they schedule regular operator breaks to reduce fatigue. After implementing these solutions, defect rates drop by 85%, saving significant costs and improving product quality.
By addressing risks at both the design and process levels, FMEA empowers organizations to create robust products and efficient production systems. In the next section, we’ll explore the detailed methodology of conducting an FMEA, step by step. Stay tuned!
3. The FMEA Methodology: A Step-by-Step Guide
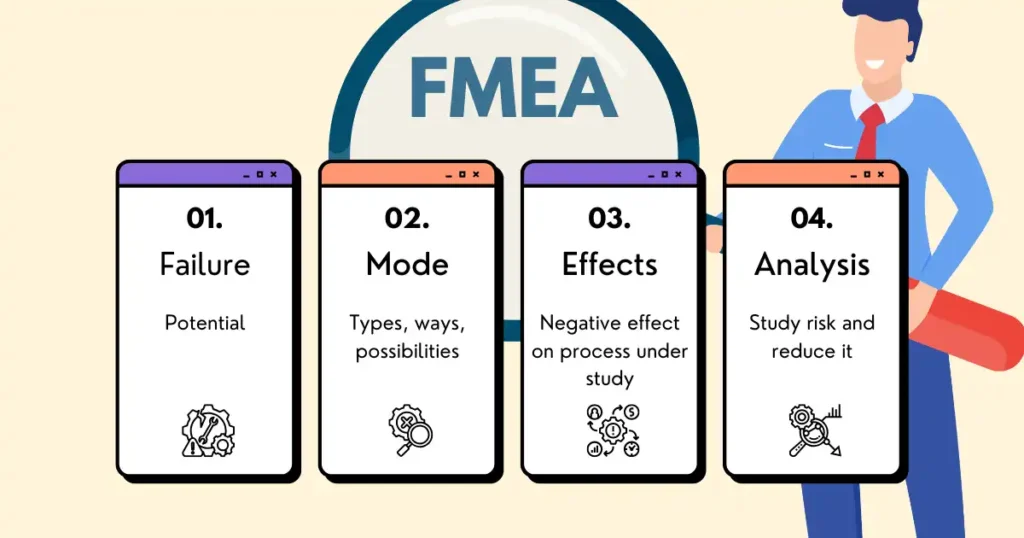
Failure Mode and Effects Analysis (FMEA) is a structured methodology designed to proactively address risks and prevent potential failures. Each step in the FMEA process is essential to building a robust, failure-resistant system. Let’s break it down into actionable steps.
3.1 Assembling the Right Team
The foundation of a successful FMEA lies in its team. A cross-functional team brings diverse perspectives and expertise, ensuring no potential failure is overlooked. Why is this important? Because failure modes often arise from complex interactions between components, processes, and environments.
Who should be on the team?
- Design engineers: Understand product specifications and limitations.
- Process engineers: Familiar with operational workflows.
- Quality assurance specialists: Ensure compliance with standards and identify risks.
- Production staff: Provide insights into real-world challenges during manufacturing.
- Customers or end-users: Share expectations and potential use-case scenarios.
Tips for team composition:
- Choose representatives from diverse departments to foster collaboration.
- Ensure all members are familiar with the FMEA process and objectives.
- Designate a skilled facilitator to lead discussions and manage timelines.
Collaboration is key. As the saying goes, “None of us is as smart as all of us.”
3.2 Defining the Scope
Before diving into the analysis, it’s critical to define the scope. This step ensures clarity and focus, preventing the team from becoming overwhelmed by unrelated details.
Key considerations for scope definition:
- Level of analysis: Will the FMEA focus on a system, subsystem, or individual component?
- Boundaries: Clearly define what is included and excluded from the analysis.
- Objectives: Identify the purpose of the FMEA—improving safety, enhancing reliability, or meeting compliance.
Practical tools to define scope:
- Flowcharts: Visualize the system or process to identify critical points of failure.
- Hierarchical diagrams: Break down the system into subsystems and components for a clear analysis structure.
For example, in a car manufacturing project, a DFMEA might focus on the braking system as a whole, while a PFMEA could zoom in on the assembly process for brake pads.
3.3 Identifying Potential Failure Modes
This step is where brainstorming meets analysis. The goal is to uncover all the ways a system, process, or component could fail.
Techniques for identifying failure modes:
- Brainstorming sessions: Gather insights from team members based on their expertise.
- Historical data review: Analyze past failures and known issues.
- Fishbone diagrams (Ishikawa): Organize potential failure modes by categories like materials, methods, machinery, and environment.
Example failure modes:
- Design phase: Incorrect material selection leading to premature wear.
- Process phase: Misalignment of parts during assembly.
Encourage the team to think creatively and ask open-ended questions like, “What could go wrong?” or “How might this fail in extreme conditions?”
3.4 Assessing Effects and Severity
After identifying failure modes, the next step is to evaluate their potential effects and determine their severity.
How to assess effects:
- Identify the consequences of each failure mode. For example:
- Customer impact: Safety risks, dissatisfaction, or inconvenience.
- Regulatory impact: Non-compliance with standards.
- Operational impact: Downtime or increased costs.
Severity rating scale:
- 1: Minor inconvenience, negligible impact.
- 10: Catastrophic failure, potentially life-threatening.
For instance, a faulty airbag deployment would score a 10 due to the high risk to human safety, whereas a minor cosmetic defect might score a 2.
To ensure consistency, teams should agree on rating criteria based on the specific context of the analysis.
3.5 Analyzing Root Causes
Understanding the root causes of failures is crucial for effective prevention. This step digs deep into why failures occur.
Popular root cause analysis tools:
1. 5 Whys: Keep asking “Why?” until you uncover the root cause.
Example:
- Why did the machine stop? → A fuse blew.
- Why did the fuse blow? → The motor overheated.
- Why did the motor overheat? → Inadequate lubrication.
2. Fault Tree Analysis (FTA): Fault Tree Analysis (FTA) is a systematic, deductive process used to analyze the causes of system failures. Imagine it as a diagram resembling an inverted tree, where the “top event” (the failure) forms the trunk and various “branches” represent contributing factors.
Here’s how it breaks down:
- Top Event: The failure or undesirable event you’re analyzing.
- Intermediate Events: Contributing events that lead to the top event.
- Basic Events: Root causes, usually where the analysis stops.
FTA is used widely in industries such as aerospace, nuclear, and manufacturing to ensure safety and reliability. By understanding how different factors interact to cause failures, you can identify and mitigate risks proactively.
Focus areas for root cause analysis:
- Design flaws (e.g., material weaknesses, improper tolerances).
- Process issues (e.g., operator errors, environmental factors).
- Maintenance oversights (e.g., worn-out components).
By addressing the root cause instead of symptoms, teams ensure long-term solutions rather than quick fixes.
3.6 Assigning Risk Priority Numbers (RPN)
Risk Priority Numbers (RPNs) help prioritize failure modes based on their severity, likelihood, and detectability.
The formula:
- RPN = Severity × Occurrence × Detection
- Severity (S): Impact of the failure on safety, operations, or customers.
- Occurrence (O): Likelihood of the failure happening (e.g., 1 = rare, 10 = inevitable).
- Detection (D): Likelihood of detecting the failure before it occurs (1 = almost certain, 10 = unlikely).
For example:
- Severity = 8, Occurrence = 6, Detection = 4
RPN = 8 × 6 × 4 = 192
In recent years, many organizations have adopted Action Priority (AP) as an alternative to RPN. AP considers context and focuses on actionable outcomes rather than arbitrary thresholds.
3.7 Developing and Implementing Action Plans
The final step is turning insights into action. Once failure modes are prioritized, the team must develop and implement mitigation strategies.
Risk mitigation strategies:
- Design improvements: Modify components or materials to reduce risks.
- Process adjustments: Redesign workflows or add quality control steps.
- Preventive measures: Use error-proofing techniques, such as poka-yoke.
Example: In an electronics assembly line, a common failure mode is soldering defects. Mitigation might include:
- Installing automated soldering machines for consistency.
- Introducing inline inspections to detect issues early.
Iterative improvements: Monitor the effectiveness of implemented actions using metrics like defect rates or customer feedback. Regularly update the FMEA to reflect lessons learned and changing conditions.
As the famous quote goes, “Plans are nothing; planning is everything.” Continuous refinement ensures your FMEA remains a living document, driving proactive improvements over time.
This structured guide transforms FMEA into an actionable, repeatable process. By following these steps, teams can systematically address risks, ensuring safer, more reliable products and processes.
4. Advanced FMEA Techniques and Trends
As industries evolve and become more complex, traditional FMEA methodologies are being enhanced with advanced technologies and modern frameworks. This section explores the integration of AI, innovative risk assessment approaches, and the application of FMEA in emerging industries.
4.1 Integration with AI and Machine Learning
The rise of artificial intelligence (AI) and machine learning (ML) has revolutionized risk analysis, making FMEA smarter and more proactive than ever before. Predictive analytics, powered by AI, allows organizations to anticipate failures before they happen, saving significant time and resources.
Predictive Analytics in FMEA
Traditional FMEA relies on historical data and human intuition, which can sometimes lead to overlooked failure modes. AI changes this by analyzing vast datasets, uncovering hidden patterns, and forecasting failure probabilities. For example:
- AI can detect wear-and-tear patterns in industrial machines by analyzing sensor data, predicting potential failures weeks or months in advance.
- Machine learning algorithms can simulate various failure scenarios under different conditions, offering insights that would be impossible to uncover manually.
AI-Enhanced Detection Controls
One of the core elements of FMEA is detectability. AI enhances this by leveraging real-time monitoring tools, such as:
- Computer Vision: AI-driven cameras can identify defects on production lines instantly, reducing reliance on human inspectors.
- IoT Sensors: Internet of Things (IoT) devices monitor equipment performance in real-time, alerting teams to anomalies before failures occur.
- Natural Language Processing (NLP): AI can analyze maintenance logs and customer feedback to identify recurring issues that might otherwise be missed.
These advancements not only increase detection accuracy but also free up human resources to focus on strategic improvements. As AI continues to evolve, the possibilities for its application in FMEA are virtually limitless, ensuring products and processes become safer and more reliable.
4.2 Beyond RPN: Modern Risk Assessment Approaches
While the Risk Priority Number (RPN) has been a cornerstone of FMEA, its limitations are becoming increasingly apparent in today’s dynamic environments. Modern approaches such as Action Priority (AP) and fuzzy logic are gaining traction for more nuanced risk evaluations.
Transition from RPN to AP
In 2019, the AIAG-VDA FMEA Handbook introduced AP as a more reliable alternative to RPN. Unlike RPN, which multiplies severity, occurrence, and detection rankings, AP focuses on actionable outcomes. This shift:
- Eliminates rank reversals, a common criticism of RPN.
- Prioritizes critical issues based on safety and compliance, not just mathematical scores.
For example, a high-severity failure mode might require immediate action regardless of its detectability, a nuance that RPN often overlooks.
The Case for Fuzzy Logic in Risk Evaluation
Fuzzy logic uses linguistic variables (e.g., “high,” “medium,” “low”) to assess risks more flexibly. This approach:
- Addresses the subjectivity inherent in scoring systems.
- Allows for a more dynamic and holistic understanding of risks. For instance, instead of assigning a rigid 7/10 to “probability of failure,” fuzzy logic considers the range of conditions under which this probability may change.
Both AP and fuzzy logic reflect a shift toward risk assessment methods that are more adaptable and reflective of real-world complexities.
4.3 FMEA in Emerging Industries
As industries like healthcare, the Internet of Things (IoT), and renewable energy expand, they bring unique challenges that require tailored FMEA applications. These sectors are particularly sensitive to risks due to the high stakes involved, making FMEA a critical tool.
Healthcare
In healthcare, FMEA ensures patient safety by analyzing potential failures in medical devices, procedures, and software systems. For example:
- Hospitals use FMEA to prevent medication errors by analyzing dispensing processes.
- Medical device manufacturers apply PFMEA to identify and mitigate risks in production lines for life-saving equipment like ventilators.
The growing reliance on AI-driven diagnostic tools also introduces new failure modes, such as algorithmic bias or data integrity issues, which FMEA must address.
Internet of Things (IoT)
IoT-enabled devices operate in highly interconnected ecosystems, where a single failure can cascade through the network. Key applications of FMEA in IoT include:
- Identifying security vulnerabilities, such as potential hacking points in smart home systems.
- Assessing hardware reliability under varying environmental conditions, such as extreme temperatures or humidity.
Renewable Energy
In renewable energy, FMEA is vital for ensuring the reliability of solar panels, wind turbines, and energy storage systems. For instance:
- Solar panel manufacturers use DFMEA to assess risks like material degradation under UV exposure.
- Wind turbine operators rely on PFMEA to optimize maintenance schedules, preventing downtime caused by mechanical failures.
Each of these industries presents unique challenges, from ensuring regulatory compliance in healthcare to managing cybersecurity risks in IoT. By adapting FMEA to these contexts, organizations can proactively address risks and build trust with stakeholders.
The integration of advanced technologies like AI, the adoption of modern risk assessment approaches, and the application of FMEA in emerging industries demonstrate how this methodology continues to evolve. Whether it’s predicting failures with AI or adapting to the unique demands of IoT, FMEA remains a vital tool for ensuring safety, reliability, and innovation across industries.
FMEA: Failure, Modes, Effects, Analysis | Certification Course
Buy Now for $13.99
Udemy prices may vary depending on applied coupons and promotional events.
- 🧑🏫 29 lectures
- ⌚ 2h 3m total length
- 🗃️ 6 downloadable resources
- 📜 Certificate of completion
- 👩🎓 12,634 students
- ⭐ 4.7 rating by 482 students
We offer a detailed breakdown of RPN in our highest-rated Failure Modes and Effects Analysis (FMEA) course on Udemy. If you’re interested in exploring other tools within the FMEA methodology, consider enrolling in our course.
5. Common Pitfalls in FMEA Implementation
Despite its proven benefits, Failure Mode and Effects Analysis (FMEA) can fall short of expectations if not implemented correctly. Many organizations encounter pitfalls that undermine the effectiveness of their FMEA process, often leading to overlooked risks or wasted resources. Understanding these pitfalls and adopting strategies to address them is key to maximizing the value of FMEA.
1. Lack of Cross-Functional Involvement
One of the most common mistakes in FMEA implementation is failing to assemble a truly cross-functional team. When only a single department, such as engineering or quality assurance, drives the analysis, the process can become siloed and miss critical perspectives. For example, production staff may notice operational inefficiencies that engineers overlook, while customer service representatives might provide insights into common end-user complaints.
Strategy to Avoid:
- Ensure diverse representation from design, engineering, quality, production, and customer-facing teams.
- Foster collaboration through structured brainstorming sessions where every member contributes.
- Use a skilled facilitator to mediate discussions and prevent any one perspective from dominating.
2. Over-Reliance on RPN Without Holistic Context
The Risk Priority Number (RPN) has been a cornerstone of FMEA, but over-reliance on it can lead to skewed priorities. For example, a low-severity but high-occurrence issue may end up deprioritized due to its low RPN, even though it poses a significant cumulative risk. Similarly, teams may focus only on numerical thresholds rather than understanding the broader implications of failures.
Strategy to Avoid:
- Use Action Priority (AP) instead of RPN to guide decision-making, as it considers safety and compliance more effectively.
- Supplement quantitative scores with qualitative discussions to ensure critical issues aren’t overlooked.
- Regularly review rankings to identify misalignments between scores and real-world risks.
3. Insufficient Updates to FMEA as Systems Evolve
FMEA is often treated as a one-and-done exercise, leading to outdated analyses that fail to address changes in design, processes, or operating conditions. This oversight can result in undetected risks and vulnerabilities over time.
Strategy to Avoid:
- Treat FMEA as a living document that evolves with the system it analyzes.
- Establish regular review schedules, especially during major milestones such as design revisions, process updates, or regulatory changes.
- Use digital tools to centralize FMEA documentation and streamline updates across teams.
By addressing these common pitfalls, organizations can ensure their FMEA process remains robust, relevant, and effective. The key lies in fostering collaboration, moving beyond rigid reliance on metrics, and treating FMEA as a dynamic, iterative tool. As the saying goes, “A failure avoided is a success achieved”—and FMEA’s potential to prevent failures hinges on how well it is implemented and maintained.
6. Tools and Templates for FMEA
The effectiveness of Failure Mode and Effects Analysis (FMEA) depends not only on the methodology but also on the tools and templates used to streamline the process. From powerful commercial software to free open-source solutions, the right tools can simplify data collection, improve collaboration, and make the FMEA process more efficient. Below, we’ll explore some popular options, discuss tools for small and medium enterprises (SMEs), and introduce a customizable FMEA template created specifically for this blog.
Popular Software Solutions for FMEA
Many organizations use specialized software to manage FMEA processes, offering features that go beyond traditional spreadsheets. Here are some popular options:
- IQ-RM Pro
This robust software is designed for industries like automotive and aerospace. It adheres to the latest AIAG-VDA FMEA standards and provides:- Customizable forms and templates.
- Automated Risk Priority Number (RPN) and Action Priority (AP) calculations.
- Advanced reporting tools for tracking improvements.
- Integration with existing quality management systems (QMS).
- AIAG-VDA FMEA Software
Specifically tailored to the new AIAG-VDA FMEA handbook, this software provides:- Preloaded templates for Design FMEA (DFMEA) and Process FMEA (PFMEA).
- Enhanced visualization features like action priority charts.
- Support for team collaboration across departments.
- Xactium Risk Management
A cloud-based platform that combines FMEA with overall risk management. Features include:- Real-time data sharing and collaboration.
- Risk heatmaps to visualize vulnerabilities.
- Scalable options for small teams or large enterprises.
These tools are excellent for organizations that need high-level functionality, but they often come with a steep price tag, making them less accessible to smaller businesses.
Open-Source Tools for SMEs
For small and medium enterprises (SMEs) with limited budgets, open-source tools provide a cost-effective alternative. While they may lack the advanced features of commercial software, these tools are sufficient for straightforward FMEA processes.
- FMEA-Pro Lite
- A free, downloadable spreadsheet template.
- Includes basic fields for severity, occurrence, detection, and RPN calculation.
- Ideal for startups or teams just starting to implement FMEA.
- OpenFMEA
- An open-source software built specifically for SMEs.
- Allows users to create FMEA worksheets, track revisions, and generate reports.
- Features a simple interface that doesn’t require extensive training.
- Google Sheets and Excel Templates
- Many SMEs use free FMEA templates available online for Google Sheets or Excel.
- These templates are often customizable, allowing teams to adapt them to specific needs.
- Examples include templates for DFMEA, PFMEA, or combined worksheets.
While open-source tools lack advanced integrations, they provide a starting point for organizations that prioritize affordability over complexity.
A Unique FMEA Template for You
To help readers get started, we’ve created a customizable FMEA template designed to streamline your risk analysis process. This downloadable template is user-friendly and adaptable to various industries, featuring:
- Preformatted sections for DFMEA and PFMEA.
- Dropdown menus for standardized severity, occurrence, and detection ratings.
- Automatic RPN and AP calculations.
- Fields for assigning responsibilities and tracking updates.
How to Use the Template:
- Begin by filling out basic project information, such as system name and analysis scope.
- Use the dropdown menus to select ratings for each failure mode.
- Review the calculated RPN/AP scores to prioritize actions.
- Assign team members and deadlines for each mitigation strategy.
- Update the template regularly as the system evolves.
Download the FMEA Template: [Click To Download]
This free resource ensures that even small teams can perform effective FMEA without investing in costly tools.
The choice of FMEA tools depends on your organization’s needs and budget. While powerful software like IQ-RM Pro is perfect for large enterprises, open-source solutions and customizable templates offer accessible options for smaller teams. Regardless of the tool you choose, remember that FMEA’s success relies on collaboration, regular updates, and a structured approach. Take the first step today by downloading our unique template and start optimizing your risk management process!
7. Real-World Case Studies of FMEA Success
FMEA has proven its value across industries, from improving product safety to reducing operational risks. This section explores real-world examples of FMEA implementation in the automotive, aerospace, and healthcare sectors, highlighting how this methodology has led to significant advancements in safety, quality, and reliability.
7.1 Automotive Industry: Enhancing Safety and Reducing Recalls
The automotive industry has long relied on FMEA to improve safety and minimize recalls. One notable example is the implementation of FMEA by Ford Motor Company during the 1970s. After the infamous Ford Pinto case, where design flaws led to catastrophic fuel tank failures, the company adopted FMEA to prevent such issues in future models. By systematically analyzing potential failure modes in critical systems, such as braking and fuel systems, Ford was able to redesign components to improve reliability and safety.
A more recent example involves Toyota, a global leader in manufacturing excellence. Toyota utilized FMEA to address airbag deployment issues in their vehicles. Through Design FMEA (DFMEA), the company identified potential material defects and failure scenarios under extreme environmental conditions. These insights enabled Toyota to make critical changes to airbag sensors and materials, significantly reducing the risk of non-deployment or accidental deployment.
The results speak for themselves: FMEA helped Toyota lower warranty claims and strengthen consumer trust. Automotive recalls, which can cost millions of dollars and damage brand reputation, were minimized, making FMEA an indispensable tool in the industry.
7.2 Aerospace Industry: FMEA in NASA’s Apollo Missions
In the high-stakes world of aerospace, failure is not an option. FMEA played a critical role during NASA’s Apollo space missions in the 1960s, helping the agency mitigate risks and ensure mission success.
One of the most notable applications of FMEA was in the development of the Apollo Guidance Computer (AGC). This computer was responsible for navigation and control, making its reliability paramount. NASA engineers used FMEA to systematically analyze potential failure modes, such as hardware malfunctions or software glitches, and their effects on critical mission phases like lunar landing and reentry.
For instance, during the Apollo 11 mission, FMEA helped identify the risk of an overloading alarm caused by redundant processes in the AGC. While the alarm did occur during the lunar descent, preemptive analysis ensured that engineers were prepared to address it, allowing Neil Armstrong and Buzz Aldrin to safely land on the moon.
NASA’s rigorous application of FMEA extended beyond hardware, influencing procedures for launch, in-flight operations, and emergency scenarios. The success of the Apollo program demonstrated how FMEA can safeguard complex systems, making it a gold standard for risk management in aerospace engineering.
7.3 Healthcare Sector: Preventing Medical Device Failures
The healthcare industry has embraced FMEA as a powerful tool to enhance patient safety and prevent medical device failures. With lives at stake, identifying and mitigating risks is paramount.
Example: Infusion Pumps
Infusion pumps are commonly used to deliver medications and fluids to patients. However, these devices are prone to various failure modes, such as:
- Incorrect dosage due to calibration errors.
- Blocked or kinked tubing leading to interrupted flow.
- Alarm system failures, preventing timely intervention.
To address these risks, a leading medical device manufacturer conducted Process FMEA (PFMEA) during the production phase. The analysis revealed that a significant number of failures were caused by tubing material defects and inconsistent assembly practices. As a result, the company implemented stricter material quality checks and automated assembly lines, reducing failure rates by 50%.
Example: Medication Administration
Hospitals also apply FMEA to prevent medication errors. A large hospital in the U.S. used FMEA to analyze its intravenous (IV) medication administration process. The team identified several risks, including:
- Human errors during dosage preparation.
- Cross-contamination due to improper sterilization.
- Delayed administration caused by equipment malfunctions.
By addressing these issues, the hospital introduced barcode scanning for medication verification, improved staff training, and scheduled regular equipment maintenance. These changes led to a 40% reduction in medication errors within a year.
FMEA and Healthcare Standards
FMEA has become integral to regulatory compliance in the healthcare sector. The U.S. Food and Drug Administration (FDA) recommends FMEA as part of risk management for medical devices, aligning with international standards like ISO 14971.
Through its application, healthcare providers and manufacturers have achieved safer devices, reduced litigation risks, and improved patient outcomes, underscoring the importance of FMEA in protecting lives.
These case studies highlight the transformative impact of FMEA across diverse industries. From enhancing automotive safety to ensuring the reliability of space missions and safeguarding patient health, FMEA consistently proves its value as a proactive risk management tool. By learning from these successes, organizations can better harness FMEA to drive innovation, improve quality, and build trust in their products and processes.
8. Limitations of FMEA and Complementary Approaches
While Failure Mode and Effects Analysis (FMEA) is a powerful risk management tool, it is not without limitations. Understanding its shortcomings and exploring complementary techniques can help organizations build a more comprehensive and effective risk mitigation strategy.
Limitations of FMEA
Despite its strengths, FMEA faces several challenges that can hinder its effectiveness if not addressed:
1. Incomplete Data
- FMEA heavily relies on historical data and expert knowledge. However, in many cases, especially for new products or technologies, sufficient data may not be available. This can lead to incomplete or inaccurate identification of potential failure modes.
- Example: In emerging industries like IoT, where devices and systems are rapidly evolving, it can be challenging to anticipate failure scenarios based on past trends.
2. Time Constraints
- Conducting a thorough FMEA can be time-intensive, particularly for complex systems. Teams may feel pressured to rush the process, resulting in overlooked risks or insufficient analysis.
- Example: In fast-paced industries such as consumer electronics, time-to-market pressures may lead to an incomplete FMEA that misses critical failure modes.
3. Scope Issues
- Defining the scope of an FMEA is crucial but often difficult. A scope that is too broad can overwhelm the team, while one that is too narrow may miss significant risks.
- Example: In an automotive application, focusing solely on the braking system without considering its interaction with other systems (e.g., electronics and hydraulics) may lead to gaps in the analysis.
4. Over-Reliance on Numerical Scoring
- The Risk Priority Number (RPN) method, while useful, has limitations. RPN scores may fail to capture the real-world implications of certain failure modes, especially those with high severity but low occurrence.
- Example: A rare failure in a medical device that poses a life-threatening risk may receive a low RPN and be deprioritized.
Complementary Techniques
To address these limitations, organizations often pair FMEA with other risk assessment methods. These complementary techniques provide different perspectives and enhance the overall analysis.
1. Fault Tree Analysis (FTA)
- What it is: FTA is a top-down approach that starts with a specific undesirable event (e.g., system failure) and works backward to identify all possible causes.
- How it complements FMEA: While FMEA focuses on individual failure modes, FTA provides a broader view by showing how multiple failures can combine to cause a system-level event.
- Example: In aerospace engineering, FTA can be used alongside FMEA to analyze how individual component failures might lead to a catastrophic event, such as engine failure during flight.
- What it is: Hazard Analysis identifies potential hazards (sources of risk) and evaluates their likelihood and impact. It is often used in safety-critical industries.
- How it complements FMEA: While FMEA analyzes risks at the component or process level, Hazard Analysis focuses on identifying external risks and system-wide hazards.
- Example: In the healthcare sector, Hazard Analysis can assess risks associated with environmental factors, such as contamination during surgical procedures, which might not be captured in an FMEA.
- What it is: Bow-Tie Analysis visualizes risk pathways by showing the relationship between potential causes, preventive measures, consequences, and mitigation strategies. It is shaped like a bow tie, with the hazard in the center.
- How it complements FMEA: Bow-Tie Analysis excels at visually demonstrating how preventive and mitigation controls interact, helping to bridge gaps left by FMEA.
- Example: In the oil and gas industry, Bow-Tie Analysis can illustrate how equipment failures, human errors, and environmental factors might lead to an explosion, as well as the controls in place to prevent or minimize damage.
Building a Comprehensive Risk Management Strategy
By combining FMEA with complementary techniques, organizations can address its limitations and gain a more holistic view of risks. For example:
- Use FMEA to identify specific failure modes at the component level.
- Apply FTA to evaluate how these failures might escalate into system-level risks.
- Perform Hazard Analysis to identify broader threats and their impact on the overall system.
- Implement Bow-Tie Analysis to visually map preventive and mitigation strategies.
While FMEA remains an essential tool for risk management, its limitations underscore the need for a more integrated approach. Complementary techniques like FTA, Hazard Analysis, and Bow-Tie Analysis provide additional layers of insight, ensuring that risks are thoroughly analyzed and effectively mitigated. By leveraging these methodologies together, organizations can create a robust risk management framework that is both proactive and comprehensive.
9. The Future of FMEA
The future of Failure Mode and Effects Analysis (FMEA) is poised to be shaped by evolving standards, technological advancements, and its growing role in global challenges like sustainability. As industries strive for greater reliability and adaptability, FMEA will continue to adapt, becoming an even more integral part of risk management frameworks.
Evolving Standards: AIAG-VDA and Beyond
The release of the AIAG-VDA FMEA Handbook marked a significant shift in how FMEA is approached. This harmonized methodology combines best practices from the American and German automotive industries, providing a structured framework that emphasizes action priority (AP) over traditional Risk Priority Number (RPN). The adoption of these standards is expected to expand beyond automotive, influencing other industries like aerospace, healthcare, and electronics.
Future updates to these standards are likely to incorporate advanced tools such as AI-driven analytics and digital integration, ensuring that FMEA remains relevant in increasingly complex systems.
Role of FMEA in Sustainability and Green Initiatives
As sustainability becomes a global priority, FMEA is set to play a crucial role in designing eco-friendly products and processes. By identifying failure modes related to resource consumption, energy efficiency, and environmental impact, organizations can align their operations with green initiatives.
For instance, renewable energy companies are already using FMEA to improve the durability of solar panels and wind turbines, reducing waste and ensuring long-term reliability. Similarly, manufacturers are leveraging FMEA to minimize material waste and optimize energy usage in production.
Predictions for the Next Decade
The next decade will likely see FMEA evolve in the following ways:
- Integration with digital twins: Real-time simulations will allow teams to test failure modes virtually, leading to more accurate predictions and faster iterations.
- AI-enhanced insights: Machine learning models will predict risks dynamically, offering actionable recommendations with minimal human intervention.
- Wider adoption in emerging industries: From autonomous vehicles to IoT ecosystems, FMEA will become essential in managing the complexity and interconnectedness of modern systems.
The future of FMEA lies in its ability to evolve and adapt, ensuring its continued relevance in a rapidly changing world.
FMEA: Failure, Modes, Effects, Analysis | Certification Course
Buy Now for $13.99
Udemy prices may vary depending on applied coupons and promotional events.
- 🧑🏫 29 lectures
- ⌚ 2h 3m total length
- 🗃️ 6 downloadable resources
- 📜 Certificate of completion
- 👩🎓 12,634 students
- ⭐ 4.7 rating by 482 students
We offer a detailed breakdown of RPN in our highest-rated Failure Modes and Effects Analysis (FMEA) course on Udemy. If you’re interested in exploring other tools within the FMEA methodology, consider enrolling in our course.
10. Conclusion
Failure Mode and Effects Analysis (FMEA) is more than just a tool—it’s a mindset that empowers organizations to proactively identify and address risks before they escalate. From its origins in the military to its current role in industries like automotive, aerospace, healthcare, and beyond, FMEA has proven to be a cornerstone of quality and reliability. By following its structured methodology, organizations can enhance safety, improve efficiency, and foster innovation.
Throughout this guide, we’ve explored FMEA’s evolution, methodology, applications, and future trends. The integration of advanced technologies like AI and digital twins, coupled with modern risk assessment approaches, ensures that FMEA will remain vital for years to come. Whether it’s streamlining design processes or mitigating environmental impact, FMEA equips organizations with the foresight to navigate complexities in today’s fast-paced world.
Why wait to embrace proactive risk analysis? Organizations that prioritize FMEA can reduce failures, save costs, and build trust with customers. Take the first step today by downloading the customizable FMEA template provided in this blog. Need expert assistance? Contact our team for consultation and personalized solutions tailored to your industry.
FAQ: Common Questions About FMEA
What industries benefit most from FMEA?
FMEA is widely used in automotive, aerospace, healthcare, manufacturing, consumer electronics, and renewable energy sectors. Its applications are versatile, making it beneficial for any industry focused on safety, reliability, and quality improvement.
What is the difference between DFMEA and PFMEA?
Design FMEA (DFMEA) focuses on identifying risks in the design phase, such as material defects or geometry issues. Process FMEA (PFMEA), on the other hand, addresses risks in the manufacturing or assembly process, such as operator errors or equipment malfunctions.
How often should an FMEA be updated?
FMEA should be treated as a living document. It should be updated whenever there are design changes, process updates, new regulations, or when feedback from customers or operations identifies new risks.
Can small businesses implement FMEA without expensive software?
Absolutely! Small businesses can use free or open-source FMEA templates to get started. While advanced software offers additional features, basic FMEA can be effectively managed using Excel or Google Sheets.
What is the difference between RPN and AP in FMEA?
Risk Priority Number (RPN) is calculated as the product of severity, occurrence, and detection ratings, while Action Priority (AP) focuses on the urgency of addressing issues, particularly those related to safety and compliance, without relying solely on numerical thresholds.
How does FMEA align with sustainability goals?
FMEA can identify risks related to resource efficiency, energy consumption, and environmental impact, helping organizations design greener products and processes.
What are the biggest challenges in implementing FMEA?
Common challenges include defining the scope, ensuring cross-functional collaboration, and maintaining the FMEA document over time. Using complementary tools and strategies can help overcome these hurdles.