Turn Waste into Value—Fast.
Earn an industry-recognized Lean Six Sigma Belt online and start cutting defects, delays, and dollars lost —in less than one work-day.
Pick Your Belt, Level-Up Your Process
Compare duration, price, and real-world wins—from the free White Belt to advanced Lean Management—and jump into the training that delivers your fastest ROI.
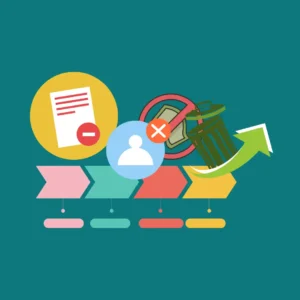
The 8 Wastes of Lean
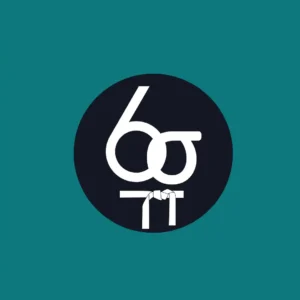
Lean Six Sigma White Belt: Certification
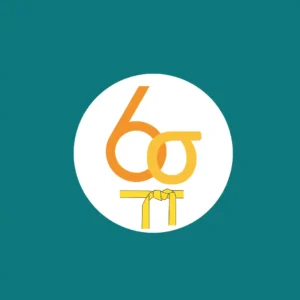
Lean Six Sigma Yellow Belt: Certification
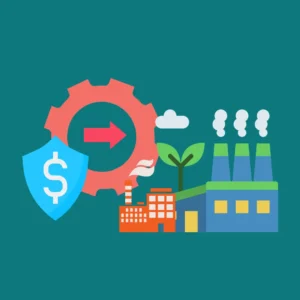
Lean Management: Certification
Udemy list prices fluctuate with promotions and may vary by region.
Our Instructor
Robert Chapman
Why Lean Six Sigma?
✅ Become an in-demand improvement expert.
✅ Elevate efficiency while boosting customer value.
✅ Recognized world-wide across every industry vertical.
White-to-Black Belt holders average +$42,000 to +$130,000 salaries.
Industry & Function Application
Lean Six Sigma turns every process into a measurable, improvable asset.
Lean Six Sigma in Business Function
Human Resources
Cut time-to-hire by mapping each approval loop, error-proof onboarding docs with check-sheets, and shrink voluntary turnover through voice-of-employee (VoE) surveys analysed with Pareto charts.
Research & Design (R&D)
Shorten concept-to-prototype by running DOE-based sprints, slash re-work with FMEA, and capture lessons learned in a real-time knowledge base.
Sales & Marketing
Reduce quote-to-cash lead-time, reveal root causes of stalled deals with 5 Whys, and convert A/B results into DMAIC improvements that lift win-rates.
Accounting & Finance
Close the books days earlier by mistake-proofing reconciliations, visualise cash-application flow in a SIPOC, and spot cost leaks via value-stream cost analysis.
Procurement / Supply Management
Shrink RFQ cycle-time, renegotiate with data-driven cost-of-quality reports, and stabilise deliveries through supplier capability indices (Cpk).
IT & Software Development
Eradicate repeat defects with root-cause retros, speed backlog flow using Kanban + Little’s Law, and benchmark uptime with statistical control.
Logistics & Supply Chain
Eliminate stock-outs and excess inventory via takt-time alignment, ‘milk-run’ scheduling, and statistical demand forecasting.
Production / Operations
Drive OEE up and scrap down through SMED changeovers, 5S workplace organisation, and in-line SPC dashboards.
Service & Customer Support
Cut ticket resolution time, design error-free hand-offs with swim-lane mapping, and turn VoC feedback into DMAIC quick-wins that lift NPS.
Maintenance & Facilities
Move from reactive fixes to predictive uptime by pairing FMEA with condition-based monitoring and Weibull failure modelling.
Quality & Regulatory
Reduce non-conformances, increase first-pass yield, and automate evidence gathering for audits with visual dashboards.
Product Management
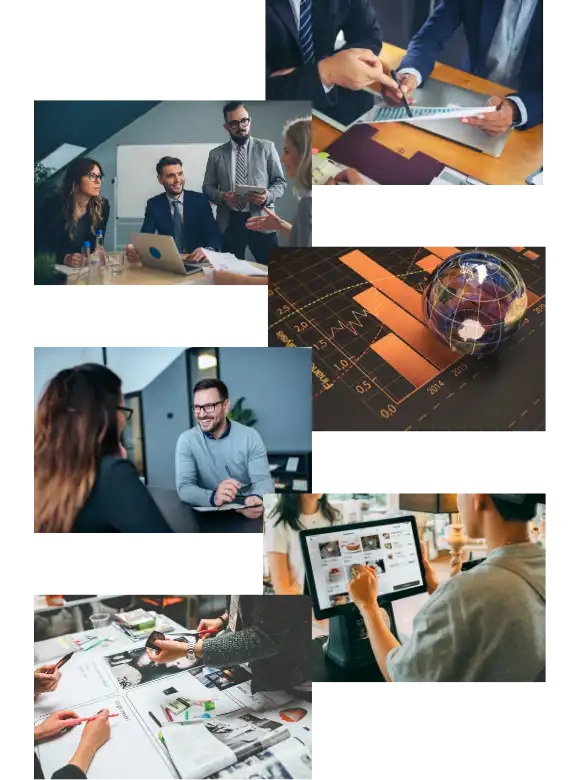
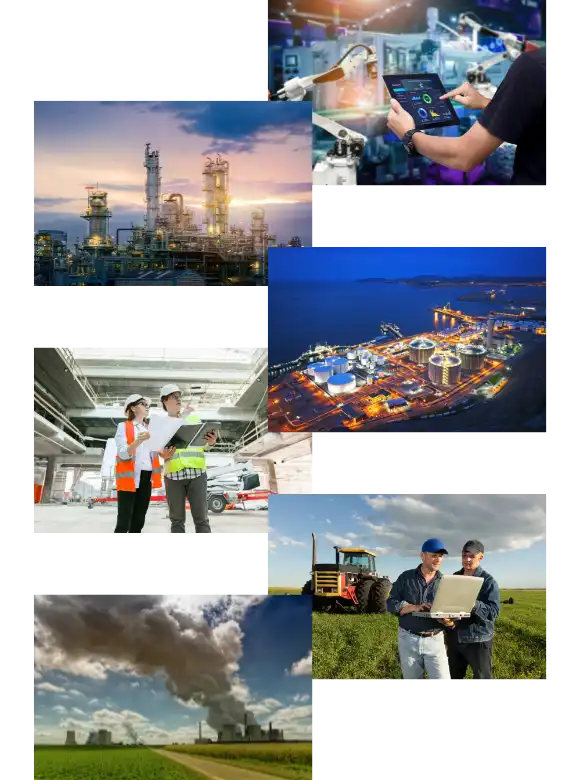
Lean Six Sigma in Industry
Agriculture & Agri-business
Optimise planting-to-harvest workflow, trim water and fertiliser waste, and increase yield consistency with SPC on soil metrics.
Automotive & Aerospace
Boost first-time-right assembly, reduce warranty claims through robust PPAP/APQP gates, and stabilise supply with PFMEA-driven risk control.
Construction & Infrastructure
Compress critical-path schedules, visualise trade hand-offs in Last Planner® pull plans, and cut re-work incidents via error-proof check-lists.
Education & EdTech
Streamline admissions, course scheduling, and financial-aid reviews; redeploy saved hours to student engagement initiatives.
Energy & Utilities
Reduce unplanned downtime, improve asset reliability, and data-log field defects for predictive maintenance analytics.
Financial Services & Insurance
Slash KYC/AML processing time, lower claim rework, and visualise fraud patterns with Pareto heat-maps.
Food & Beverage
Increase line throughput, meet HACCP/FSMA compliance, and trim changeover losses for fresher, faster delivery.
Government & Public Sector
Cut permit lead-times, standardise citizen touch-points, and show transparent ROI on taxpayer funds with before-and-after metrics.
Healthcare & Life Sciences
Reduce patient wait-times, medication errors, and OR turn-around, while meeting Joint Commission & GMP requirements.
Hospitality & Leisure
Smooth guest check-in/out, standardise housekeeping cycles, and transform feedback loops into rapid Kaizens that raise RevPAR.
Logistics & Transportation
Debottleneck hubs, cut empty-mile costs, and stabilise ETA accuracy using SPC dashboards and route DMAIC.
Manufacturing
Elevate first-pass yield, shorten lead-time, and embed a zero-defects culture across mixed-model lines.
Mining & Metals
Increase equipment availability, cut haul-truck idle, and reduce incident frequency with data-driven cycle analysis.
Pharma & Biotech
Accelerate validation batches, reduce deviations, and ensure GMP compliance with robust statistical control.
Retail & E-Commerce
Optimise pick-pack-ship flow, reduce cart-abandon rates, and use real-time dashboards to balance labour and demand.
Telecommunications
Minimise service activation time, improve network uptime, and use DMAIC to root-out chronic ticket causes.
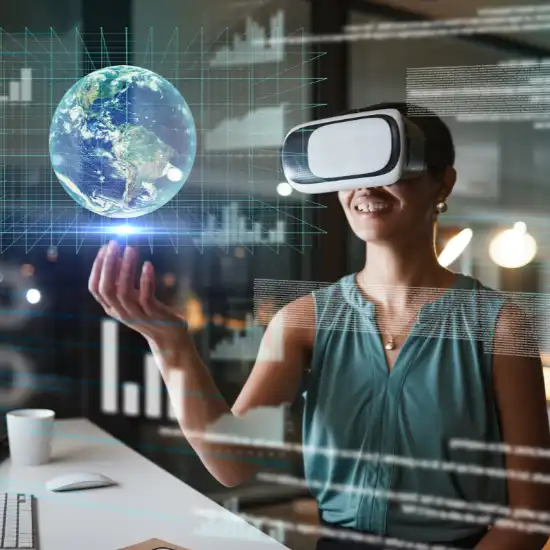
What’s Next: Lean Six Sigma 4.0
IoT & Smart Sensors
Live feeds populate control charts, letting teams react to variation before defects occur.
Real-Time Dashboards & AI Analytics
Automated anomaly alerts surface hidden waste and predict bottlenecks days in advance.
Digital Twin Modelling
Safely A/B-test process tweaks virtually—cutting trial-and-error cost and disruption.
Predictive & Prescriptive Analytics
Machine-learning models forecast downtime or demand swings so you can schedule proactively.
Augmented-Reality Work-Instructions
Overlay standard work steps on equipment, slashing set-up errors and training time.
Agile / DevOps Synergy
Marry DMAIC root-cause depth with rapid, iterative sprints for faster, locked-in gains.
Smart Factory Solutions – Beyond the Belt
Frequently Asked Questions
Do the certificates ever expire?
No. As our training promises, “Our Certifications NEVER Expire,” so once you earn a belt it stays on your résumé for life.
How long will I have access to the course materials?
Every Udemy-hosted course includes Full Lifetime Access to the videos, quizzes, and downloadable templates, so you can revisit lessons whenever new projects pop up.
Is there a money-back guarantee?
Yes. All courses come with Udemy’s 30-Day Money-Back Guarantee, giving you a no-risk window to make sure the content fits your goals.
Do I need to complete a live project to get certified?
For the White Belt, absolutely not—its requirements are simply passing multiple open-book exams (70 % minimum) and “No project requirement.” Higher belts recommend projects to cement your skills, but they’re not mandatory for issuing your course certificate.
Are the courses accredited or industry-recognized?
They’re Fully Accredited by The Council for Six Sigma Certification, the world’s largest Six Sigma accrediting body, and our credentials are trusted by global brands from Coca-Cola to the U.S. Department of Defense.
What prerequisites or prior knowledge do I need?
None. Each course is “built to be open to all levels,” and the instructor works with you throughout, so beginners can dive straight in.
How are the exams delivered?
All belt exams are online, open-book, and self-proctored; score at least 70 % and your certificate is issued instantly—no scheduling or travel hassles.
Can I study at my own pace?
Yes. “Every Six Sigma course…is self-paced,” and you can even request free deadline extensions if life gets busy.
Need to upskill your team?
Contact us for in-person workshops, live online sessions, or course licenses ready to plug into your in-house LMS. Let’s build the perfect training plan together.
Our Latest Blogs
Explore Lean Six Sigma Topics
Enroll now to get up to 80% discount! Offer ends in: